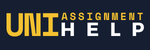
OPS928 Logistics Systems Assignment Sample
Directions to students
Start each question on a new page in a word document (and convert this word doc to a PDF for submission via Moodle). Use 12 point Times New Roman Font, 1.5-line spacing and 2.54cm margins. The length of submission is limited to 2,200 words maximum (including all answers and calculations). In your submission, please clearly mark the number of the question you are answering. There is no need to copy the questions into your submission. When answering questions, remember to define key terms and use examples where appropriate. You may use illustrations to help support your answer. It is important to demonstrate understanding and application of the relevant terms and concepts, and references are not expected. This assessment is worth 40% of your final mark. You must attain at least 50% in the final assessment and attain at least 50% overall in the subject to pass.
Section A: Case-Based Short Answer Questions (Worth 50 marks)
Question A1 (15 marks)
Orion is a global company that sells copiers. Orion currently sells 10 variants of a copier, with all inventory kept in finished-goods form. The primary component that differentiates the copiers is the printing subassembly part. Currently, Orion holds inventory of all 10 different printing subassembly parts. An idea being discussed is to introduce commonality in the printing subassembly (i.e., all 10 variants of copiers use the same common components), so that inventories can be kept in component form instead of the finished-goods form (i.e.,10 variants of copier).
(1) This conforms to the concept of postponement, which has been discussed in this subject.
Discuss the concept first, and then discuss how it can help Orion in its operations and logistics management. Be specific in your answer. (9 marks)
(2) For Orion, compared to the case when they hold inventory in finished-goods form, how will (a) and (b) below change after using common components for all variants? i.e., will each of them increase, decrease, or remain the same? Explain why. (6 marks)
(a) The response time to customer orders
(b) Safety inventory level.
Question A2 (15 marks)
During the COVID-19 pandemic, many places have seen people rushing to supermarkets for daily essentials such as toilet paper, especially when there was a recent breakout in the local area. That has led to empty shelves and stock-outs for a prolonged period of time in many supermarkets, even though the supermarkets and the product suppliers reassured that there is sufficient production capacity.
(1) Related to the different types of costs associated with inventory, explain the rationale of people hoarding products during COVID-19. (9 marks)
(2) From a logistics and supply chain perspective, discuss two reasons explaining why supermarkets experienced stockout for a considerable period of time, when the suppliers had sufficient production capacity. (6 marks)
Question A3 (20 marks)
Below is a short description of a case company. Read it and answer the questions.
Trans Move is a company providing logistical services for businesses to manage the supply chain. The services they provide include warehouse management, order fulfilment, distribution and shipping orders, and thus cover inbound flow, outbound flow, and return management. On top of transportation of freight, Trans Move also manages the distribution of freight for some clients. In some cases, Trans Move stores and manages a client’s products in Trans Move’s warehouses and decides when to ship the orders, as long as the order fulfilment meets the client’s requirements.
(1) The manager of Trans Move found that one of the key challenges is effectively managing its operations in the presence of variability. State two key sources of variability faced by Trans Move. For each source of variability, explain how the variability makes Trans Move’s operations challenging and discuss ways to reduce the impact of variability. (10 marks)
(2) One client of Trans Move is a local supermarket, for which Trans Move provides freight transportation and delivery services, and one thing to negotiate in this relationship is the freight rate. In the class, we have discussed seven economic drivers that influence transportation rate.
They include:
(1) Distance;
(2) Weight;
(3) Density;
(4) Stow ability;
(5) Handling;
(6) Liability;
(7) Market condition.
From the above list, select two factors and discuss how each of them could impact determination of freight rate for Trans Move. At least one factor should be selected from (4) – (7). (10 marks) 2023 October OPS928, Trimester 3, 2023 Page 2 of 4
Section B: Calculation-Based Questions (Worth 30 marks)
Question B1 (15 marks)
Jones Company is comparing two alternative shipping carriers to move its containers. The value of the containers is $40,000. Carrier 1 takes 4 days to ship the containers and gives a quote of $300 for the shipment. Carrier 2 takes 5 days to ship the containers and gives a quote of $260 for the shipment.
(1) Which carrier should Jones Company use, if it seeks to choose the carrier with the lowest cost? Why? The inventory holding cost for these containers is estimated to be 15% of the value per year. Assume there are no other cost differences across remaining logistics functions. Please show your calculation steps in your answer. (8 marks)
(2) Apart from the cost, discuss two factors that Jones Company should consider when choosing the carrier, and explain how these factors will influence the decision. (7 marks)
Question B2 (15 marks)
With the Strategic Profit Model below, answer the following questions.
(1) What is the firm’s profit margin? What is the firm’s Return on Assets (ROA)? Please show your calculation steps in your answer. (8 marks)
(2) Suppose the firm manages to reduce its inventory to 7000 and still achieve the same level of sales. Discuss the impact of this change on its Return on Assets (ROA) and overall profitability.
Solution
Question A1
Part 1
Concept of Postponement:
The concept of postponement refers to the strategy of delaying the final configuration or customization of a product until the last possible moment. This strategy is adopted to minimize the uncertainties of demand and to reduce inventory holding costs. Instead of producing and storing finished goods that may or may not meet specific market demands, companies maintain semi-finished products. Uni Assignment Help, Only when the actual demand is known are these semi-finished products customized or configured to meet the specific requirements. This approach allows for greater flexibility in responding to market changes and reduces the risks of inventory obsolescence.
Application to Orion's Operations and Logistics Management:
1. Inventory Reduction: By introducing commonality in the printing subassembly, Orion can significantly reduce its inventory levels. Instead of holding inventory of 10 different printing subassemblies, the company can focus on storing the shared components. This leads to decreased carrying costs and minimized risks of overstocking or understocking specific variants.
2. Reduced Obsolescence: With finished goods, there's a risk that some models might not sell as anticipated, leading to obsolete inventory. By delaying the final assembly, Orion minimizes the risk of being left with unwanted stock, thus reducing potential write-offs and wastage.
Part 2
(a) The response time to customer orders:
Change: Increase
Explanation: When Orion holds inventory in finished-goods form, they can directly ship out the required variant of copier once a customer order comes in, resulting in minimal delay. However, with the postponement strategy and keeping common components for all variants, the final assembly or configuration of the copier will only take place after the customer order is received. This means that after an order, Orion will have to assemble the product first, which will add to the lead time. Consequently, the response time to customer orders will increase as a result of the additional time required for final product assembly.
(b) Safety inventory level:
Change: Decrease
Explanation: When dealing with multiple finished goods, Orion would have to keep safety inventory for each of the 10 different copier variants to account for uncertainties in demand and supply. With the introduction of common components across all variants, the variety of items to keep as safety stock reduces, focusing only on the shared parts. This simplifies the inventory management process and reduces the total safety stock required. Since individual finished good variants might experience fluctuating demands, the aggregated demand for the common components will likely be more stable.
Question A2
Part 1
Rationale of People Hoarding Products During COVID-19 in Terms of Inventory Costs:
1. Shortage Costs: One of the most palpable costs associated with inventory management is the cost of a stock-out or shortage cost. In the context of the pandemic, consumers internalized this concept on a personal level. The fear of facing a situation where essential items, like toilet paper, would be unavailable for an indefinite period compelled many to stock up. The perceived personal cost of being without such essentials, especially in uncertain times, can be very high, leading to hoarding behaviors.
2. Holding Costs: In inventory management, holding or carrying costs refer to the expenses associated with storing and maintaining inventory, like storage costs, insurance, and potential obsolescence. During the COVID-19 outbreak, consumers evaluated their own "holding costs" in a unique way. The inconvenience of frequent store visits during lockdowns or the risk of exposure to the virus outweighed the physical space or financial costs of hoarding. In essence, the perceived benefits of having a personal stockpile during unpredictable times seemed to outweigh the "costs" of storing those goods at home.
Part 2
From a logistics and supply chain perspective, the stockouts in supermarkets during the COVID-19 pandemic, despite suppliers having adequate production capacity, can be attributed to the following reasons:
1. Bullwhip Effect: This phenomenon describes the amplification of demand fluctuations as one moves up the supply chain, from the retail end to distributors, manufacturers, and raw material suppliers. In the context of the pandemic, even a small increase in consumer buying at the retail level could translate into much larger perceived demand spikes up the chain. Suppliers and manufacturers, trying to adjust to these perceived spikes, might then over-produce or over-ship, causing disruptions and inefficiencies.
2. Supply Chain Constraints and Lead Times: While the production capacity for products like toilet paper was sufficient, the entire supply chain was not necessarily geared for such a sudden surge in demand. There's a fixed lead time involved in transporting goods from the factory, to the distributor, and finally to the retail shelves. The logistics infrastructure, including trucks, drivers, and warehousing facilities, faced bottlenecks due to the unexpected surge in volume.
Question A3
Part 1
Sources of Variability Faced by Trans Move:
1. Demand Variability:
Challenge: Trans Move operates in a domain where the demands of clients can fluctuate based on market trends, seasons, promotions, or even global events (like a pandemic). Demand variability can make it challenging to predict the exact amount of storage space needed, the resources required for order fulfillment, and the transportation and distribution mechanisms to be deployed. Such unpredictability can lead to inefficiencies, overstocking, understocking, and delays.
Ways to Reduce Impact:
o Demand Forecasting: By using advanced data analytics and artificial intelligence tools, Trans Move can predict demand trends based on historical data and market analysis. A good forecasting model can provide insights into future demand, allowing for better resource allocation.
o Flexible Warehousing: Adopting modular and scalable warehousing solutions can ensure that the space can be adjusted based on demand. Collaborative relationships with other logistics providers can also help in temporarily increasing storage capacity during high-demand periods.
2. Operational Variability (e.g., Transportation Delays, Warehouse Operations, etc.):
Challenge: The logistical domain is rife with uncertainties, such as vehicle breakdowns, traffic delays, or warehouse operational issues. Such uncertainties can impact the timely fulfillment of orders, which in turn affects the client's trust and the reputation of Trans Move.
Ways to Reduce Impact:
o Redundancy in the System: Having a backup plan or resources (like extra vehicles or a secondary delivery route) can mitigate the impact of unexpected operational delays.
o Real-time Monitoring: Implementing a robust system that provides real-time information on vehicle locations, warehouse operations, and order status can help in early identification of potential issues. Early detection can lead to quicker resolution and can allow the company to communicate proactively with clients.
Part 2
1. Distance:
Impact on Freight Rate: Distance is a primary determinant of transportation rates in logistics. The longer the distance, the higher the fuel consumption, vehicle wear and tear, driver costs, and time investments. As distance increases, the cost associated with making a delivery also rises, which is often directly translated into the freight rate.
For Trans Move, when determining rates for the local supermarket, the distance between the warehouse (or point of origin) and the supermarket (or delivery destination) will be a foundational factor. Routes that are longer or that involve complex terrains, multiple stops, or areas with frequent congestion will typically have higher rates.
2. Stowability:
Impact on Freight Rate: Stowability pertains to how easily goods can be stored within a transport vehicle. Items that are irregularly shaped, or that can't be stacked, require more space, reducing the overall efficiency of the vehicle's carrying capacity. In some cases, certain goods may require special storage conditions, such as separation from other items due to potential contamination risks or damage.
For Trans Move, when determining rates for the supermarket, they would assess the products' stowability. If the supermarket supplies products with challenging dimensions or those requiring unique stowage conditions, it would make the transportation less efficient, thus potentially increasing the freight rate. For instance, if a supermarket sends a lot of fragile items that can't be stacked, the transport vehicle might not be used to its maximum capacity, leading to inefficiencies and higher costs.
Section B: Calculation-Based Questions
Part 1
To decide which carrier offers the lowest cost, we need to consider both the direct shipping costs and the inventory holding costs associated with each option.
Step 1: Calculation of the daily holding cost The inventory holding cost for the containers per year is 15% of $40,000, which is:
0.15/$40000 = $6000
Given there are typically 365 days in a year, the daily holding cost would be:
6000/365 =16.43
Step 2: Calculation of the total cost for each carrier
Carrier 1: Shipping time: 4 days Shipping cost: $300
Total holding cost for Carrier 1 = 4 times *16.44 = $65.76
Total cost for Carrier 1 = Shipping cost + Holding cost Total cost for Carrier 1
= $300 + $65.76
= $365.76
Carrier 2: Shipping time: 5 days Shipping cost: $260
Total holding cost for Carrier 2 = 5 times* $16.44
= $82.20
Total cost for Carrier 2 = Shipping cost + Holding cost Total cost for Carrier 2
= $260 + $82.20 = $342.20
Step 3: Compare the total costs
Carrier 1's total cost = $365.76 Carrier 2's total cost = $342.20
Given that Carrier 2 has lower combined shipping and holding cost of $342.20 compared to Carrier 1's $365.76, Jones Company should choose Carrier 2 if it seeks to choose the carrier with the lowest cost.
Part 2
When choosing a carrier, several factors beyond just cost should be considered to ensure a holistic and optimal decision. Here are two important factors that Jones Company should weigh:
1. Reliability and On-time Delivery:
• Importance: A carrier's ability to consistently deliver goods on time is crucial. Delays can disrupt Jones Company's operations, potentially leading to stockouts, unsatisfied customers, or additional costs. Consistent tardiness can strain the relationship between the company and its clients or partners, especially if strict delivery timelines or contractual obligations are in place.
• Influence on Decision: If one carrier, despite being slightly more expensive, has a proven track record of on-time deliveries while the other does not, Jones Company might opt for the more reliable carrier to safeguard its reputation and maintain smooth operations. The potential costs associated with late deliveries could far outweigh the immediate savings from a cheaper, less reliable carrier.
2. Quality of Service and Handling:
• Importance: The manner in which goods are handled during transit can affect their condition upon arrival. Poor handling can result in damaged goods, leading to returns, claims, and potential loss of business. Additionally, the overall service experience, which includes communication, responsiveness to issues, and ease of doing business, plays a significant role in establishing a long-term relationship with a carrier.
• Influence on Decision: If Carrier 1, for instance, has newer vehicles, better-trained staff, advanced tracking systems, and a reputation for handling goods with care, Jones Company might lean towards them even if they are slightly more expensive. Investing in a carrier that ensures goods arrive in pristine condition and provides superior service can reduce long-term costs related to damages and streamline communications.
Question B2
Part 1
1. Profit Margin Calculation:
Profit Margin=Net Profit/Sales
From the diagram: Net Profit = Gross Margin - Total Expenses Total Expenses = Variable Expenses + Fixed Expenses Gross Margin = Sales - Cost of Goods Sold
Given: Sales = $250,000 Cost of Goods Sold = $100,000
Variable Expenses = $20,000
Fixed Expenses = $35,000
Gross Margin=250,000−100,000=150,000
Total Expenses=20,000+35,000=55,000
Net Profit:
Net Profit=150,000−55,000=95,000
Profit Margin=95,000/250,000=0.38
So, the firm's profit margin is 38%.
2. Return on Assets (ROA) Calculation:
The formula for ROA is: ROA=Net income/total assets
From the diagram: Total Assets = Current Assets + Fixed Assets Current Assets = Inventory + Accounts Receivable + Other Current Assets
Given: Inventory = $10,000 Accounts Receivable = $5,000 Other Current Assets = $5,000 Fixed Assets = $105,000
Current Assets=10,000+5,000+5,000=20,000
Total Assets=20,000+105,000=125,000
ROA=125,000/95,000=0.76
So, the firm's Return on Assets (ROA) is 76%.
Part 2
Reducing inventory without impacting sales level can have a profound effect on a firm's financial metrics, particularly its Return on Assets (ROA) and overall profitability.
1. Impact on Return on Assets (ROA): ROA estimates an organization's capacity to produce income from its assets, and it's computed as the proportion of net benefit to add up to resources. By lessening inventory, the firm declines its total assets.
In this situation, assuming that the firm figures out how to lessen its stock to 7,000, its ongoing resources will diminish by 3,000 (from 10,000 to 7,000). This decrease will prompt a reduction in the total assets. Thus, regardless of whether the net profit stays consistent, the ROA will rise, demonstrating that the organization is all the more proficiently utilizing its resources to create benefits.
2. Impact on Overall Profitability: Inventory carrying costs are a huge part of overall functional costs for some organizations. These expenses incorporate storage costs, insurance, and the cost of capital tied up in inventory. By diminishing stock, the firm can decrease these related conveying costs. This will prompt a decline in complete costs and, hence, increment the net benefit.
An increment in net profit, considering that sales stay steady, would likewise prompt an expansion in the net revenue, further supporting its overall productivity